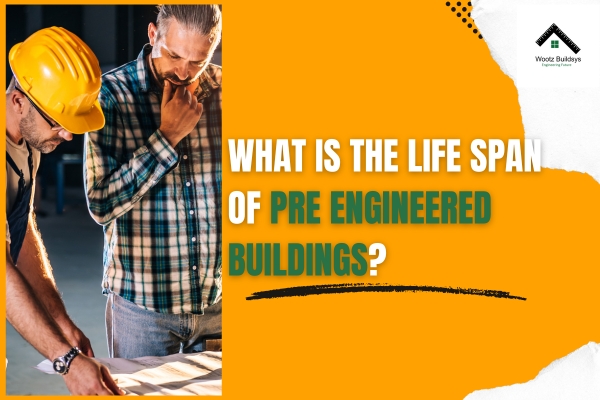
In India’s rapidly growing construction landscape, the demand for fast, durable, and cost-effective building solutions is at an all-time high. Pre Engineered Buildings (PEBs) perfectly answer this call, leading the way for factories, warehouses, commercial spaces, and even residential projects. But one question that often echoes from project owners, builders, and anyone investing in infrastructure is: What is the life span of a Pre Engineered Building? Let’s break down the facts, cut through the myths, and provide expert Indian insights in an engaging, easy-to-read format.
Understanding Pre Engineered Buildings (PEBs)
A Pre Engineered Building is a steel structure that is designed and fabricated in a factory, then assembled on-site. These buildings are popular for their speed of construction, flexibility, eco-friendliness, and—most importantly—long-lasting durability.
Why Indians Choose PEBs:
- Faster construction timelines
- Cost savings due to reduced labor and minimal material waste
- Superior design flexibility for industrial and commercial needs
- Future-ready with options for expansion or modification
What Determines the Life Span of a Pre Engineered Building?
The typical life span of a Pre Engineered Building in India ranges from 25 to 50 years or even more, depending on several critical factors:
1. Quality of Materials
- High-grade steel and corrosion-resistant coatings ensure greater longevity.
- Trusted manufacturers use top-quality materials that can withstand climatic variations across India.
2. Structural Design
- Proper engineering—factoring in water drainage, wind loads, seismic activity, and thermal movement—makes a huge difference.
- Special roof and wall details, as well as well-designed joints, help reduce wear and tear.
3. Construction Standards
- Strict quality checks during manufacturing and precise assembly at the site reduce the risk of early deterioration.
- Experienced fabricators and certified installers in India ensure your PEB is up to the mark.
4. Environmental Conditions
- Coastal areas: High humidity and salt in the air can promote corrosion—using additional protection is recommended here.
- Industrial/urban zones: Pollution and chemicals in the air may impact steel structures over time.
5. Usage and Maintenance
- Buildings used under harsh conditions (heavy loads, chemicals) require more checks and upkeep.
- Preventive maintenance—like cleaning, regular inspections, timely painting, and checking fasteners—extends the life span significantly.
- PEBs require less frequent and less expensive maintenance compared to traditional buildings.
Typical Life Span of a PEB in India
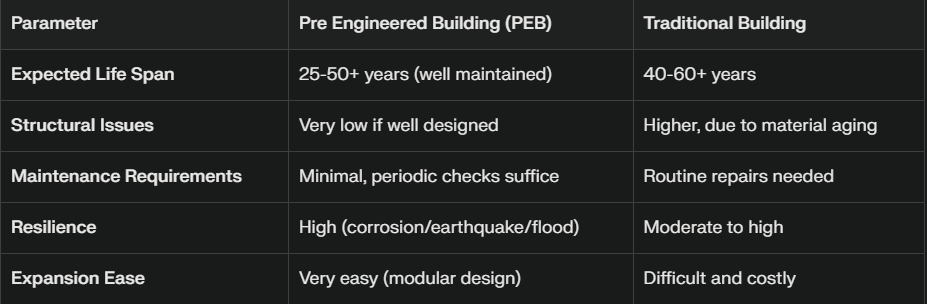
A well-designed, high-quality PEB can match or even exceed the longevity of traditional buildings if maintained properly. There are many PEBs in India still going strong after several decades, serving as testament to their reliability.
Real-World Perspective: Why PEB Life Span is a Smart Investment in India
- Industrial Use: PEBs are especially valued for factories and storage undergoing heavy, everyday use. Their steel frames stand up to intense workloads—provided regular basic checks are done.
- Weather-Resistant: Designed for India’s diverse climates, from monsoon-prone coastlines to dry interiors. Special anti-corrosive protection ensures they last in harsh environments.
- Government Projects: PEBs are widely used in infrastructure like railway stations, airports, cold storages, and public utilities—signifying government confidence in their life expectancy and reliability.
How to Maximize the Life Span of Your Pre Engineered Building
- Quality First: Always demand certified steel and branded components.
- Professional Design: Insist on reputed Indian PEB manufacturers/contractors with experience in local climatic and usage conditions.
- Periodic Maintenance: Schedule annual inspections—especially after the monsoon and before peak summer.
- Protective Coatings: Use anti-rust paint and consider galvanization in coastal areas.
- Prompt Repairs: Fix small issues (like leaks or loose fasteners) before they become major problems.
Environmental and Cost Advantages
- Sustainability: PEBs use recyclable steel, create very little site waste, and lower environmental impact compared to brick-and-mortar buildings.
- Economy: Their longer usable life and lower maintenance costs mean better returns on investment for Indian businesses and homeowners.
Addressing Common Myths
- Are PEBs “temporary” or “weak”?
Modern PEBs are engineered to last and comply with Indian engineering and seismic codes, making them robust and reliable for all types of use. - Are they costly to maintain?
On the contrary, PEBs are much easier and cheaper to maintain than conventional buildings.
Frequently Asked Questions (FAQs)
1. How long can a Pre Engineered Building actually last in India?
A quality Pre Engineered Building can last 25 to 50 years or even more, provided it is designed, built, and maintained properly. Some structures have even outlived this estimate, proving their reliable performance.
2. What can I do to increase my PEB’s life span?
Opt for reputable manufacturers, use high-quality corrosion-resistant steel, apply protective paints, and perform regular checks and basic maintenance. Addressing minor issues promptly nips long-term problems in the bud.
3. Does the climate affect the life span of a PEB in India?
Yes, especially in coastal regions (high humidity, salt air) or polluted urban areas. However, specialized coatings and design adaptations can help your building remain strong and resilient under most Indian climatic conditions.
4. Is maintenance complicated or expensive for a PEB?
Maintenance is quite simple—annual inspections and cleaning are generally enough. Costs are lower compared to traditional buildings, especially since you avoid many of the typical headaches like termite damage or concrete cracks.
5. Are PEBs suitable for residential use, or only for commercial projects?
PEBs are now used all over India for homes, offices, schools, warehouses, cold storage, community halls, and more. Their modular design, strength, and speed of construction make them an ideal, future-ready solution for almost any sector.
Conclusion
Pre Engineered Buildings have rewritten the rules on durability, cost, and sustainability for Indian builders. With a typical life span ranging from 25 to 50 years and the potential to last even longer with good care, PEBs offer a reliable, future-proof investment whether you are building a factory, warehouse, office, or even a home. As India evolves, PEBs stand out as the best answer for smart, modern construction.
cerutu4d cerutu4d cerutu4d jacktoto toto slot rtp slot jacktoto situs toto rtp live situs judi bola jacktoto sangkarbet cerutu4d cerutu4d cerutu4d jacktoto cerutu4d cerutu4d sangkarbet jacktoto panached rtp slot rtp slot situs slot situs slot rtp slot rtp slot jacktoto jacktoto jacktoto link slot link slot link slot situs toto situs toto situs toto jacktoto jacktoto jacktoto jacktoto jacktoto jacktoto jacktoto jacktoto jacktoto palembangpafi jacktoto jacktoto login cerutu4d cerutu4d prediksi hk situs slot toto slot pam4d kampungbet toto slot cabe4d cerutu4d jacktoto bandungpafi toto slot link slot resmi situs togel judi bola cerutu4d cerutu4d cerutu4d jacktoto cerutu4d cerutu4d cerutu4d cerutu4d sangkarbet cerutu4d jacktoto cerutu4d