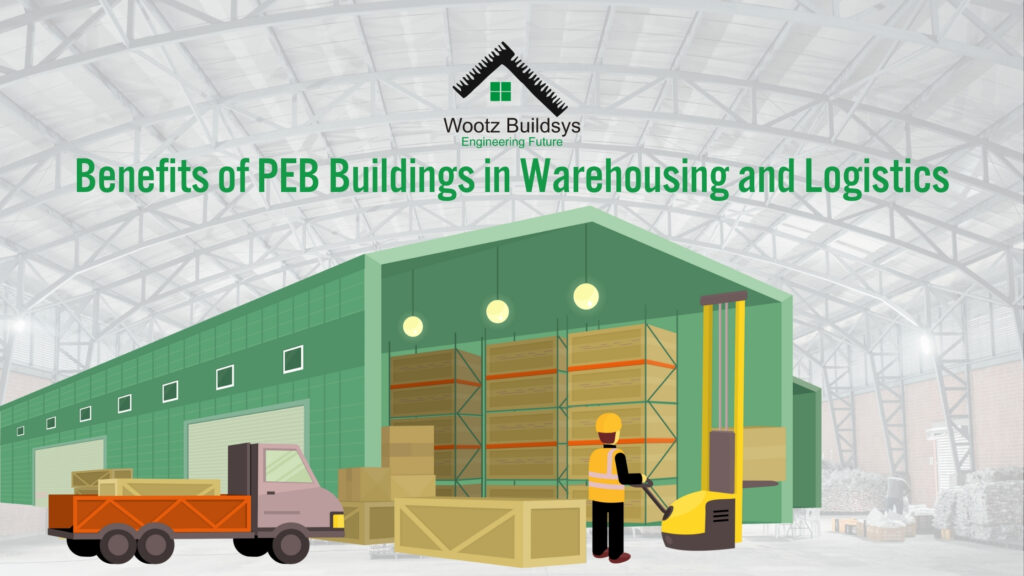
In recent years, PEB building (Pre-Engineered Building) have emerged as a game-changer in the warehousing and logistics industry. Offering cost-efficiency, durability, and flexibility, PEB building provide an innovative solution to meet the growing demand for modern storage and distribution facilities. With warehousing and logistics playing a critical role in global supply chains, the adoption of PEB building is revolutionizing how businesses operate. Let’s explore the key benefits of PEB building in this sector and why they are the preferred choice for modern infrastructure needs.
Benefits of PEB building in Warehousing and Logistics
1. Cost-Effective Construction
A major advantage of PEB building is their cost-effectiveness. In contrast to conventional construction techniques, PEB structures are pre-fabricated off-site and then assembled on-site. This streamlined process minimizes material wastage, reduces labor costs, and ensures faster project completion. For warehousing and logistics businesses operating on tight budgets, PEB building offer a highly economical alternative.
2. Faster Construction Timeline
Time is of the essence in the logistics industry, and delays can have a ripple effect across supply chains. PEB building are designed to be erected quickly due to their modular components and prefabricated nature. Compared to traditional brick-and-mortar construction, PEB building can be completed in a fraction of the time, allowing businesses to start operations sooner.
3. Customization and Flexibility
Warehousing and logistics facilities often require tailored designs to accommodate specific operational needs, such as storage racks, conveyor systems, and loading docks. PEB building offer unmatched flexibility in design, making it easy to customize the structure to suit these requirements.The modular design of PEB building allows for easy modification or expansion as business requirements change.
4. Durability and Strength
Built from high-quality steel, PEB building are known for their durability and structural integrity. They can withstand harsh environmental conditions, such as extreme temperatures, heavy rainfall, and strong winds, making them ideal for warehousing and logistics operations in diverse climates. Furthermore, PEB building are durable against pests, fire, and corrosion, guaranteeing long-term dependability.
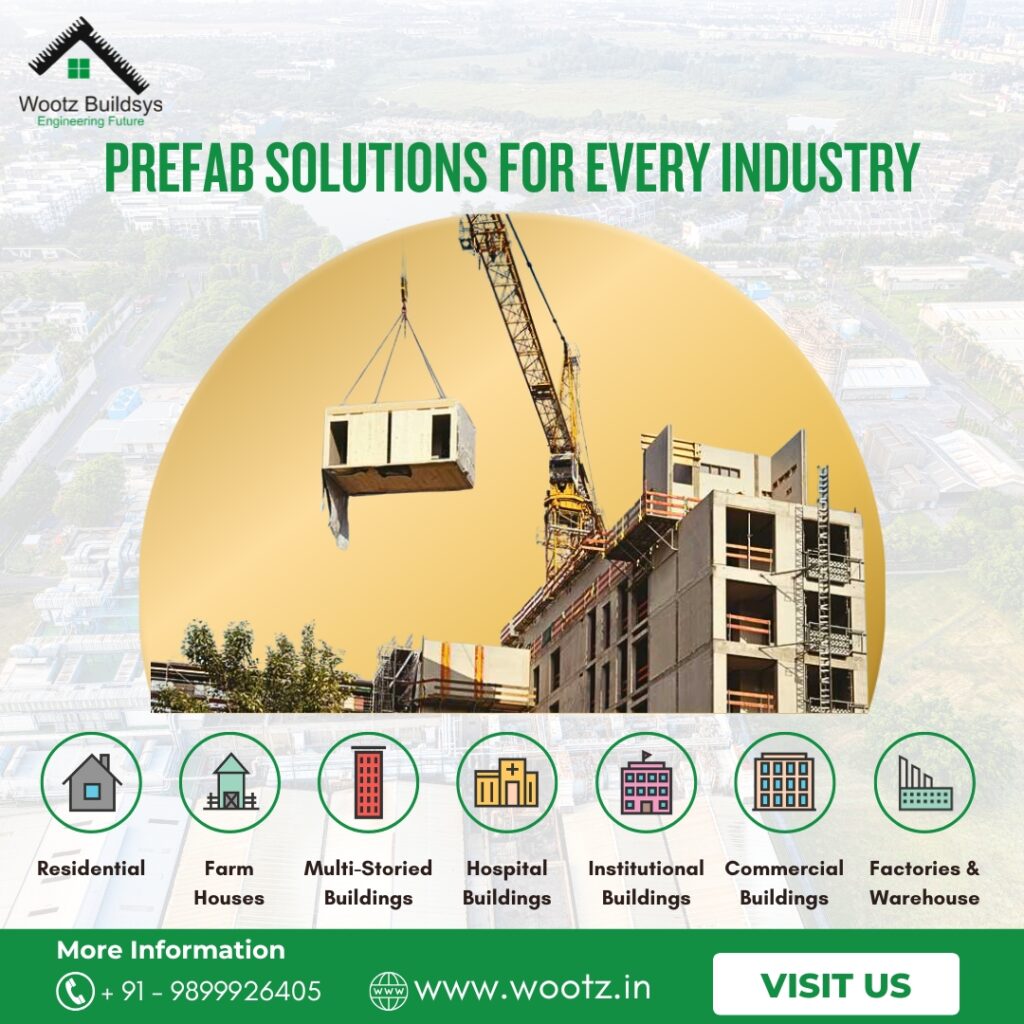
5. Energy Efficiency
Energy costs are a significant concern for warehousing facilities that operate 24/7. PEB building are constructed with a focus on energy efficiency. Features such as insulated panels, reflective roofing, and efficient ventilation systems help reduce energy consumption. These energy-efficient practices not only reduce operational costs but also support a more sustainable and environmentally-friendly future.
6. Optimal Space Utilization
Space is a premium asset in warehousing and logistics, and PEB building are designed to maximize usable space. With clear-span designs that eliminate the need for internal columns, PEB building provide unobstructed interiors, allowing for better organization and utilization of storage areas. This feature is particularly beneficial for facilities that handle large inventories or oversized goods.
7. Ease of Maintenance
Maintenance is a crucial aspect of any infrastructure. PEB building demand less maintenance than conventional structures. The use of galvanized steel and corrosion-resistant materials ensures that the building remains in excellent condition for years, reducing long-term maintenance costs.
8. Sustainability and Eco-Friendliness
Sustainability is increasingly becoming a key priority for businesses around the globe. PEB building are an environmentally friendly option due to their recyclable materials and energy-efficient designs. Moreover, the reduced construction time and minimal material wastage further enhance their eco-friendly credentials, making PEB building a sustainable choice for warehousing and logistics operations.
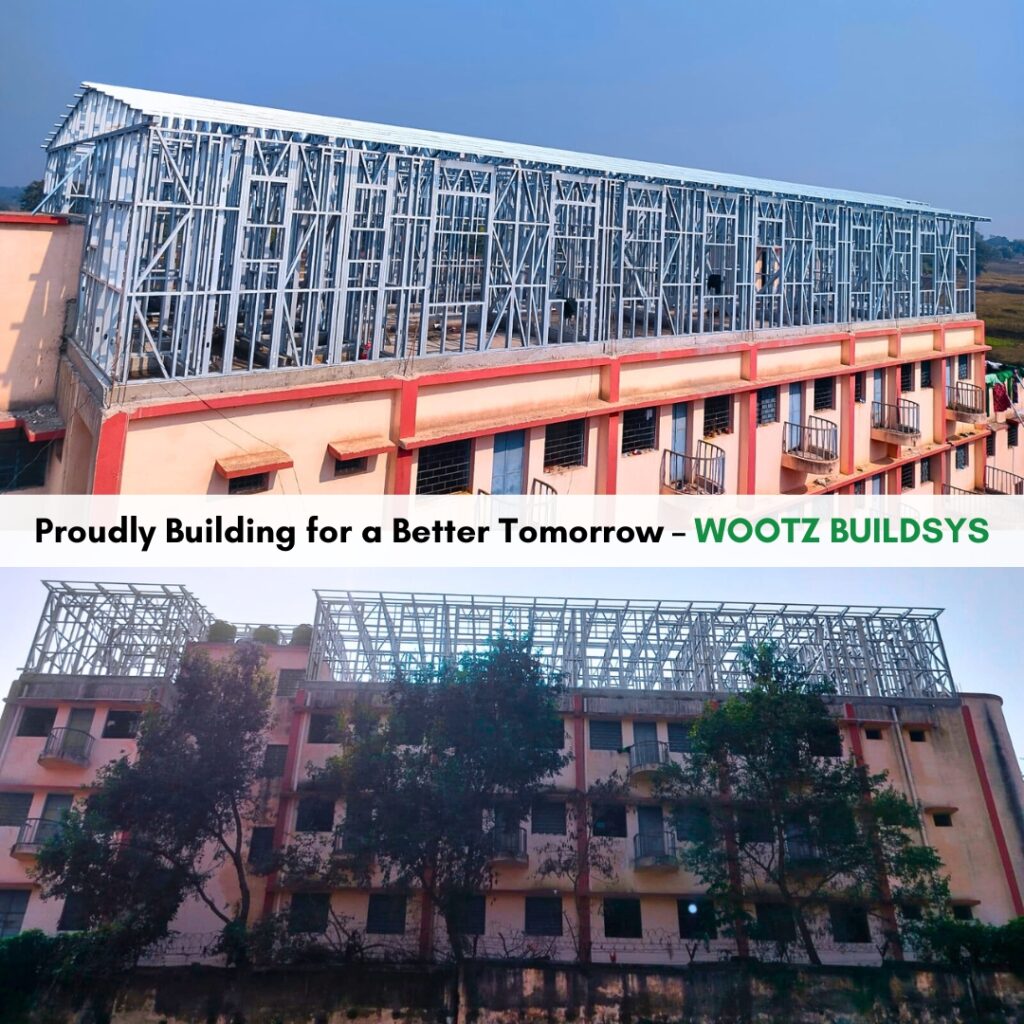
9. Scalability
As businesses grow, their infrastructure needs change. PEB building are highly scalable, allowing for seamless expansion without disrupting existing operations. This adaptability makes PEB building an ideal solution for companies looking to future-proof their warehousing and logistics facilities.
10. Compliance with Standards
Safety and compliance are essential in the logistics sector. PEB building are designed to adhere to international standards and local building codes. This ensures that the structures are safe, reliable, and capable of meeting the rigorous demands of warehousing and logistics operations.
Conclusion:
PEB building are transforming the warehousing and logistics industry by providing cost-effective, durable, and flexible infrastructure solutions. Their numerous benefits make them an invaluable asset for businesses seeking to optimize operations and stay ahead in a competitive market. Investing in PEB building is not just a smart choice but a strategic move toward building a sustainable and efficient future.
Frequently Asked Questions (FAQs)
Q1: What are PEB building?
A: PEB building are Pre-Engineered Buildings that are designed, fabricated, and assembled using prefabricated components. They are extensively used across different industries, such as warehousing and logistics.
Q2: How are PEB building different from traditional buildings?
A: Unlike traditional buildings, PEB building are prefabricated off-site and assembled on-site. They are faster to build, more affordable, and provide enhanced design flexibility.
Q3: Why are PEB building ideal for warehousing?
A: PEB building provide clear-span designs, durability, energy efficiency, and easy scalability, making them perfect for the storage and operational needs of warehouses.
Q4: Can PEB building be customized for specific needs?
A: Absolutely. PEB building offer significant design flexibility and can be tailored to meet the specific requirements of warehousing and logistics facilities.